23 May Learn Traditional Knife Making with Paul White
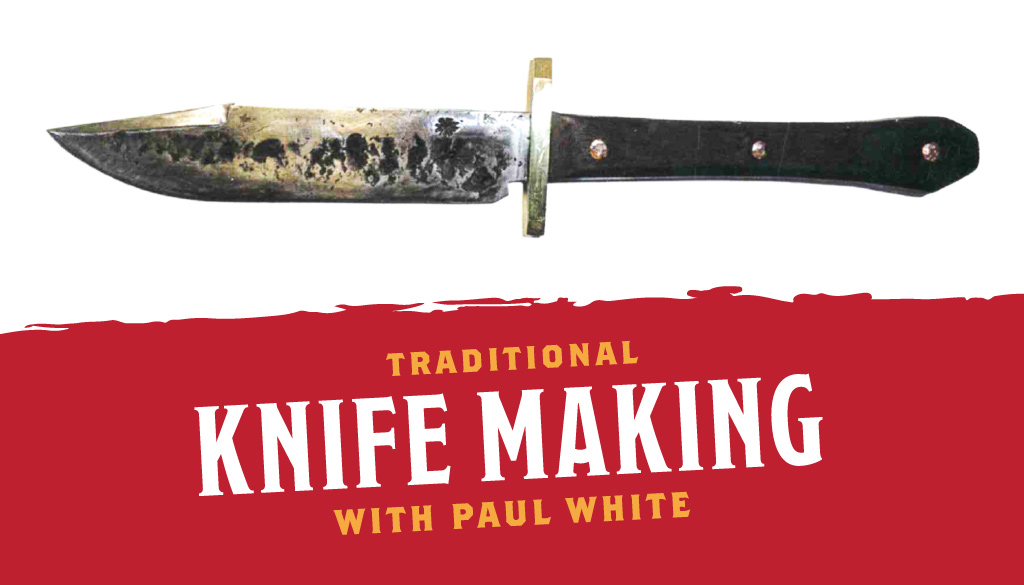
Paul White, Blacksmith and knife-maker, has forty plus years of knife-forging experience. His journey began with his exceptional good fortune by learning early from four ancient blacksmiths/knifemakers. These guys were building knives as was done before 2X72 grinders and epoxy glue. Those ageless methods taught to him by the “old
ones” he now passes to other students of the knife.
Read more about Paul White and his class in our interview below! Interested in his class? Register today to secure your spot.
Notice: This Class Has Passed. Please check out our other Blacksmithing classes.
JCCFS: Tell us more about your upcoming blacksmithing class, “Traditional Knife Making” from August 25-30, 2024.
PW: I ask the question “How did smiths make beautiful and functional knives a hundred or five hundred years ago without modern industrial bandsaws, grinders and heat-treating ovens?” The answer is “With their hammer!” I was very lucky many years ago to meet some old smiths who taught me to use basic forging skills to make a knife emerge from a hunk of steel. My Campbell students learn to shape a custom handle, form a graceful blade and set the bevel of any knife with only hammer, anvil and a few hand tools. Tempering is taught by color and eye using forge-heat alone. Smith’s then successfully attach handles with traditional riveting techniques passed to him by those same ancient smiths of a by-gone age. Anyone can make a knife given they put in the time, effort and allow someone like me to give them guidance. Down through the ages the old ones made everyday things with their hands and brains, passing those skills to their children/tribe/society. Some were generalists and others specialists. We/they made clothes, shelters, tools, weapons and all manner of necessities Today, we are no different than they we just need to shift our thinking from buying to making.
JCCFS: What can students expect to leave with?
PW: Not only will each student make a beautiful and functional Frontier knife, that will serve them and generations to come, but they will walk-out with the know-how to use those skills in building any style knife in their home forge. I bring together the history, humor, physics, art, science and blacksmith lore of knife-making. In my past life I was a children’s therapists. I try to bring measures of that experience to my interpersonal, style, patience and guidance to my students. My students use heat, smoke and arm power to pound raw metal into family heirlooms.
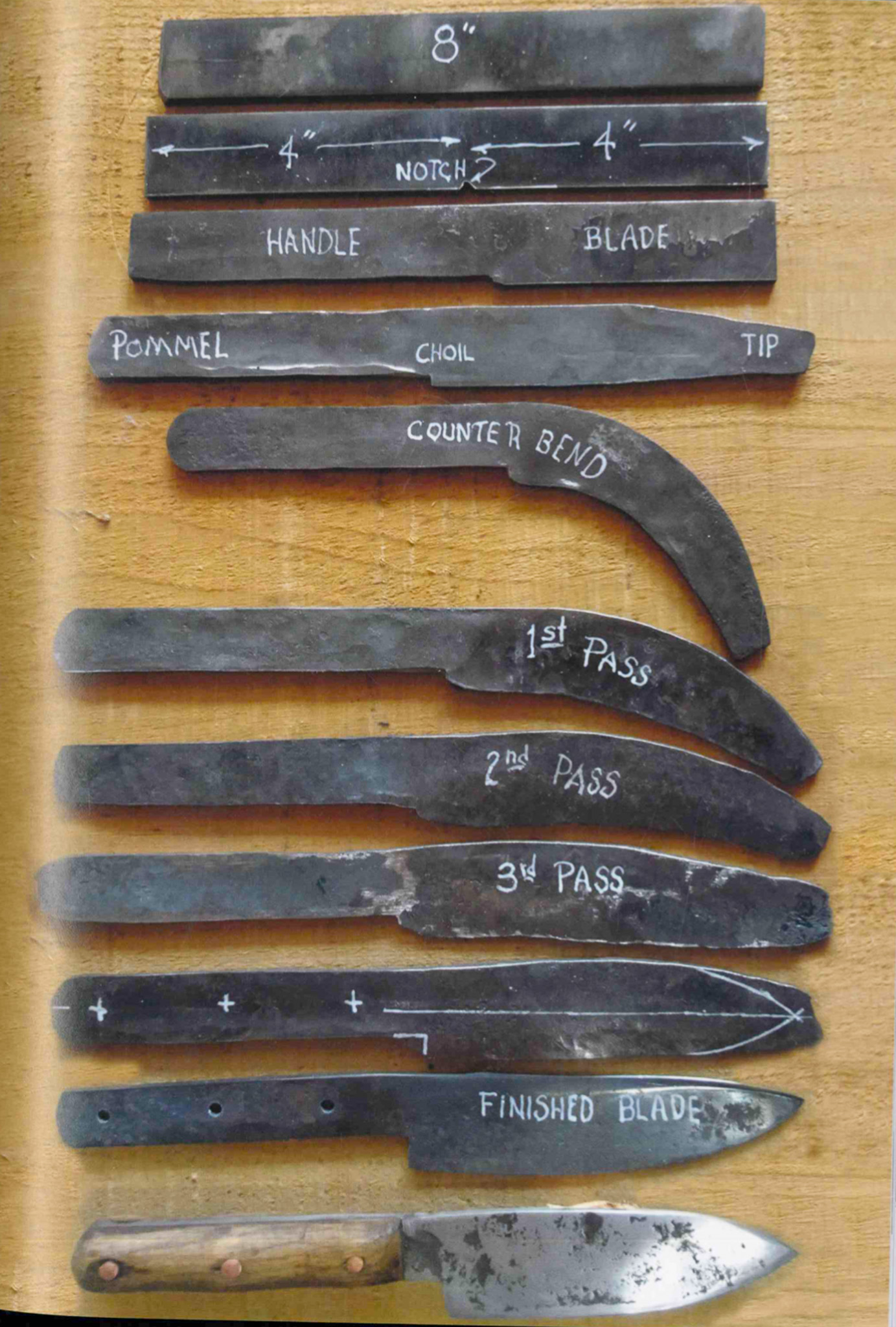
From concept to creation: transforming a billet into a blade.
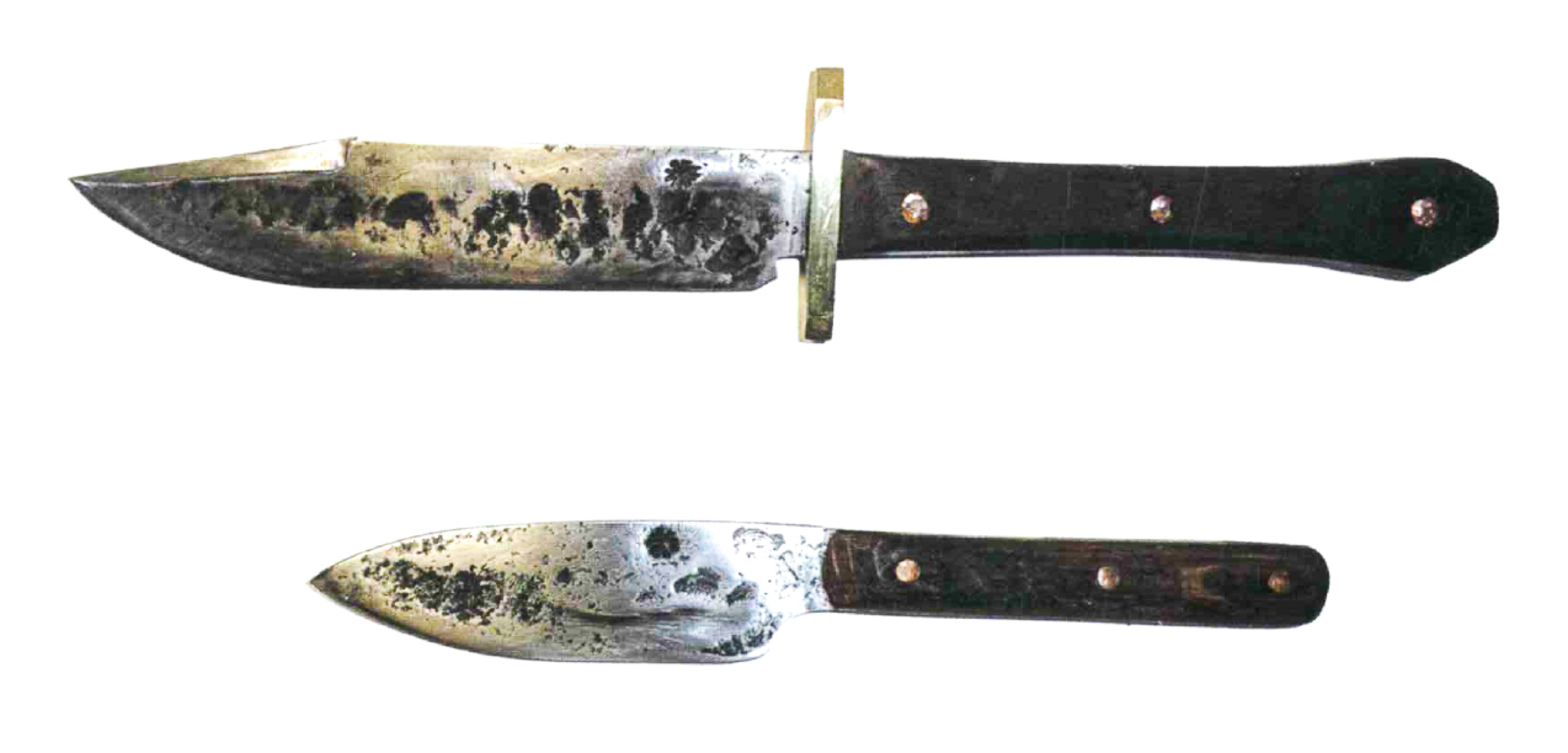
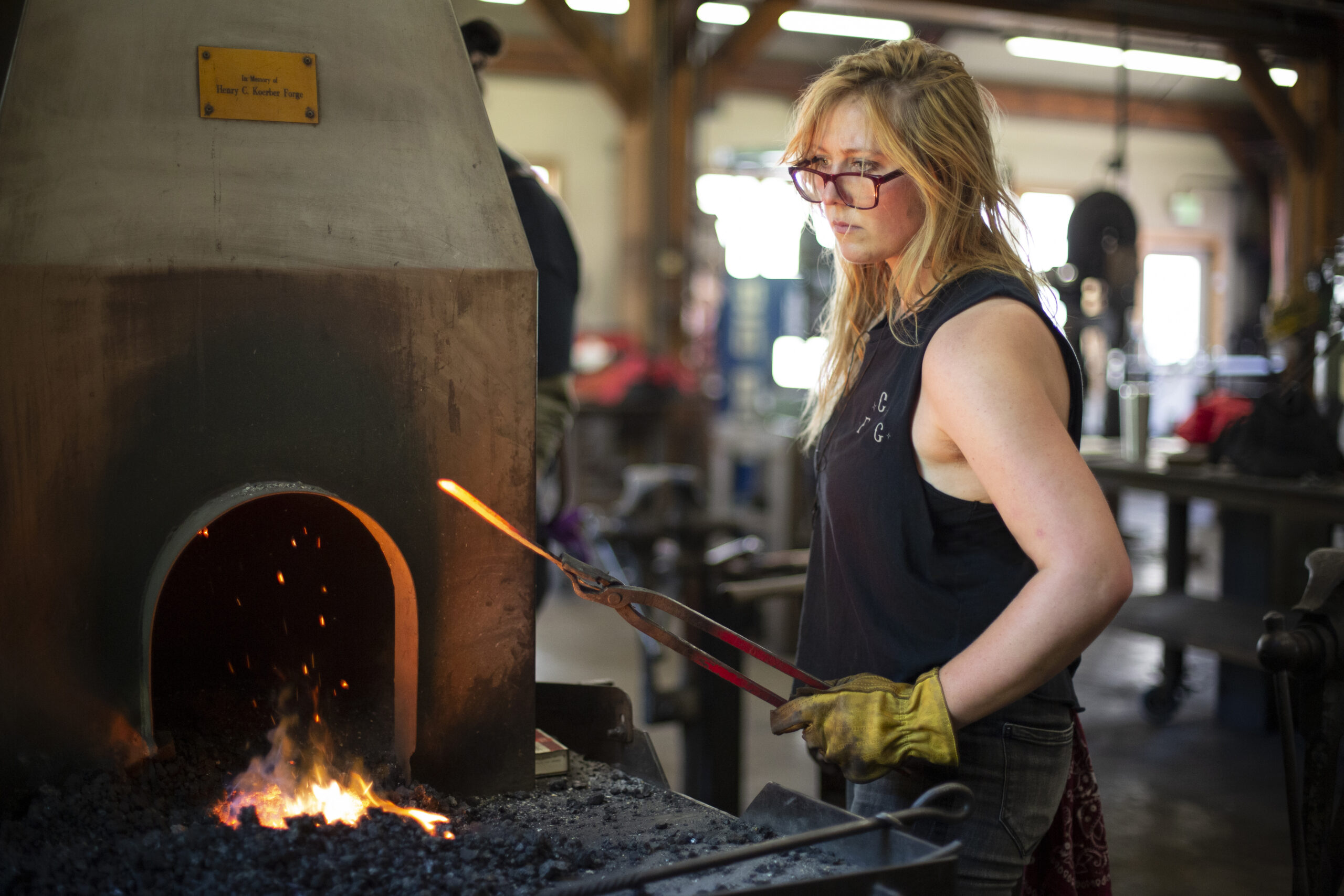
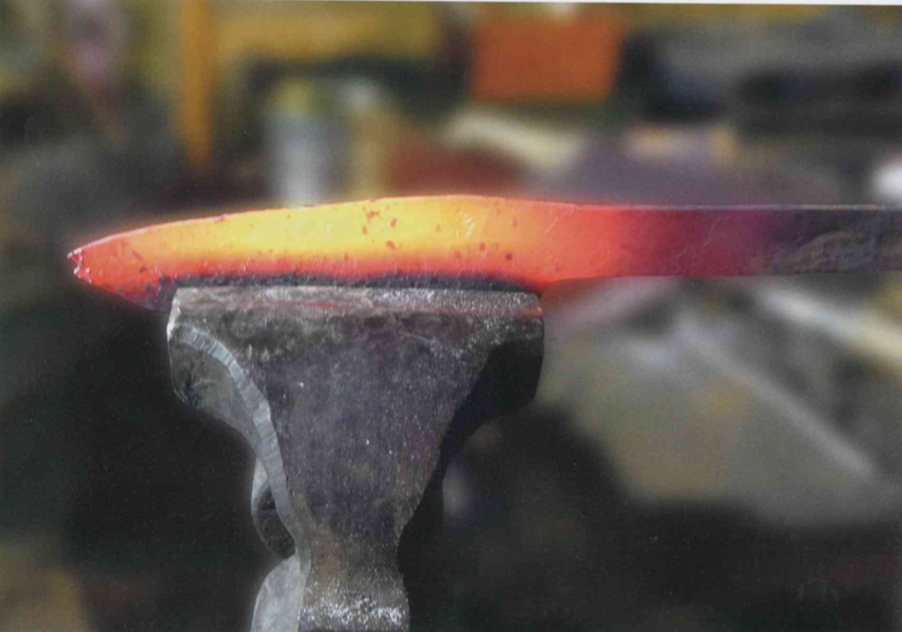
JCCFS: Tell us a little more about yourself for those who are unfamiliar.
PW: Fifty years ago, I worked with three old blacksmiths that unselfishly taught me to make knives with only hammer, anvil and a few hand tools. No belt grinders, epoxy glue or heating ovens here! You will learn to make a knife in that same method and then take home and apply that knowledge to future knife builds. Paul has taught blacksmithing and knife-building in museums, welding schools and his own shop. His book, FORGED, Making A Knife with Traditional Blacksmith Skills, is reviewed online and his videos can be seen on YouTube.
JCCFS: What do you enjoy most about teaching.
PW: Of all the joy that comes from teaching blacksmithing I most enjoy keeping the faith to Gus, Ben and Jim, those old smiths who taught me these by-gone skills. By my teaching others, I pass-on, pay forward and honor their smith-knowledge and life essence.
JCCFS: What attracted you to the Folk School? What are you most excited about for your first time teaching here?
PW: After taking a class at Campbell I was asked to teach a course. I was over-the-top about that. I had heard about and admired what they do there, from afar, for years and now I was to be a part of it all, hooray!
JCCFS: Where do you draw inspiration from for your work?
PW: Being a history buff and growing up in Virginia, my childhood was filled with “Old-Time”, Colonial Williamsburg, The Smithsonian, Gettysburg and the like. As a young adult I read The Fox Fire Series and The Mother earth News with Great relish. I began Making Windsor chairs at some point and the then the tools to make them, thus getting me into the forge, the anvil, the knife and all the talented characters I met along the way.
JCCFS: What’s one piece or craft object you’ve made recently that you are proud of, and why?
PW: Absolutely, I find, buy or otherwise acquire leaf springs from old farm wagons, buggies or buckboards. Then I forge a hunk of that 19th century carbon steel in that spring into a period knife using period skills. If someone walked into a smith shop a hundred or three-hundred years ago and asked the smith to make him a knife, they would get exactly what I make from that steel and then teach my students to make the same thing….now that’s a rush!
JCCFS: What tips would you give an aspiring craftsperson? Anything you wish you knew as a student?
PW: Enjoy what you do. Don’t expect to do it perfectly. Don’t expect to make money. Don’t expect to get it the first time. Do expect to put meaning into your life, enjoy a true inner peace and meat some wonderful people along the way.
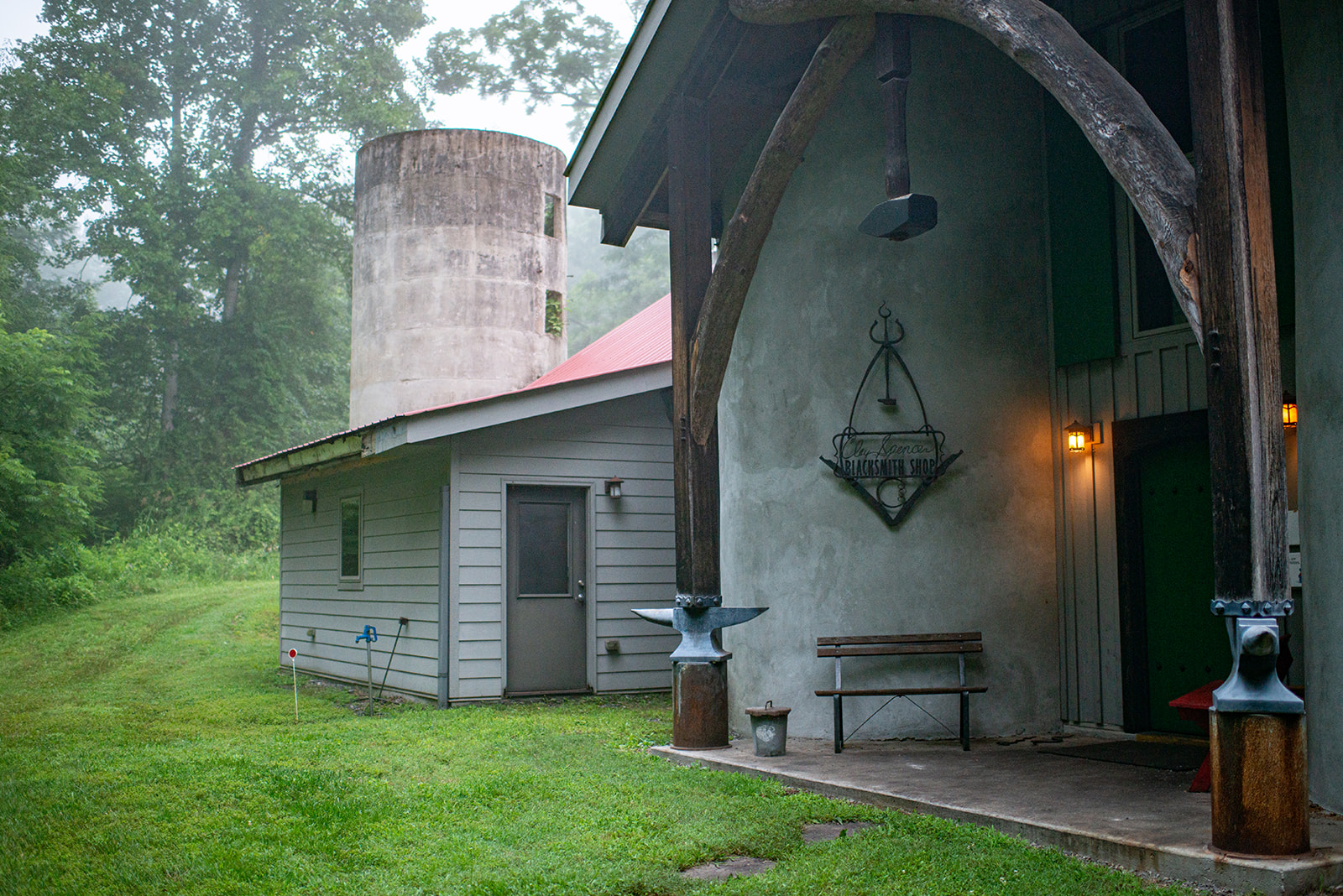
Clay Spencer Blacksmith Studio
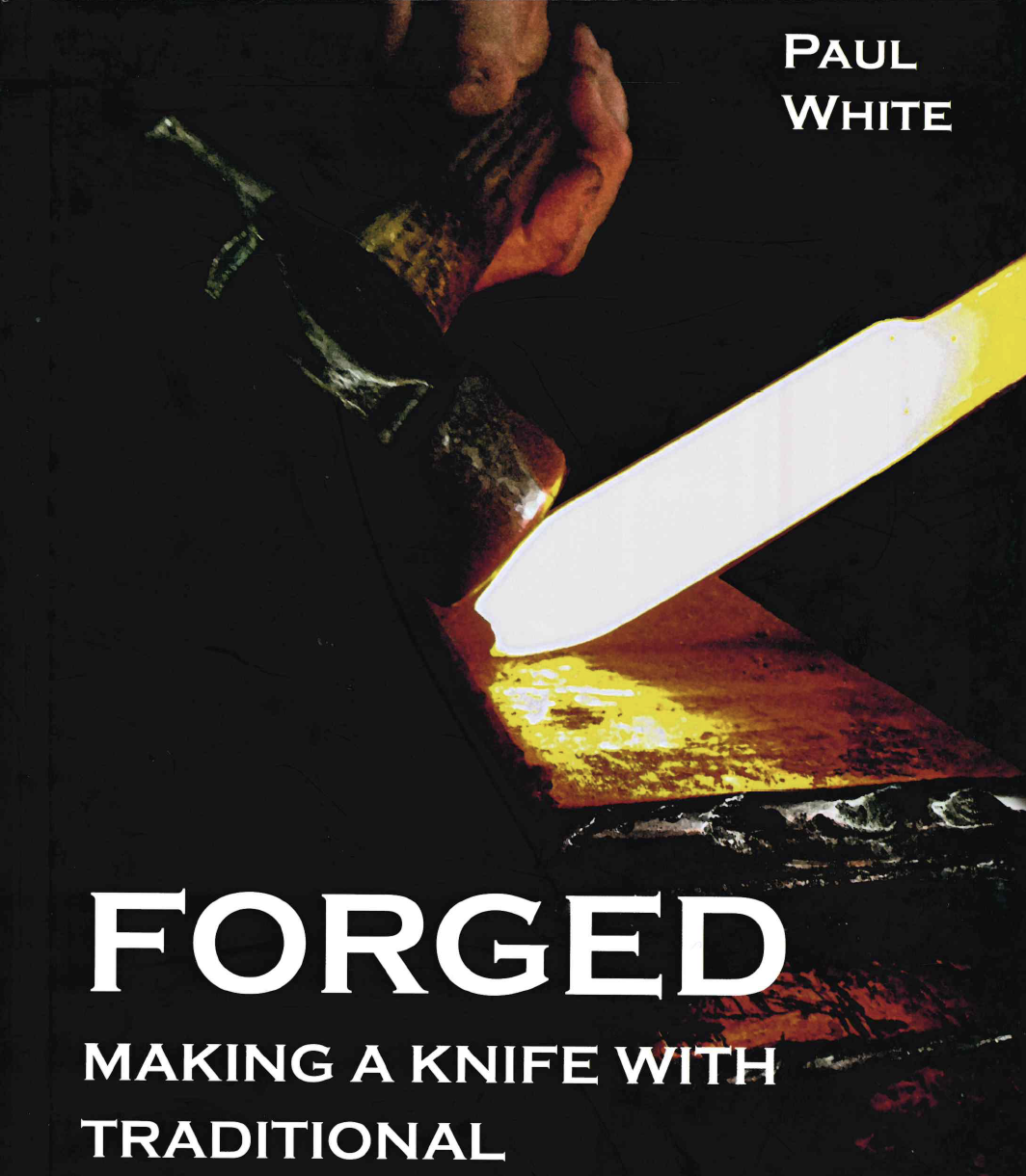
Paul White’s book “Forged Making a knife with traditional blacksmith skills” available at the Folk School Craft Shop.
Upcoming Class with Paul White
Traditional Knife Forging
Notice: This Class Has Passed. Please check out our other Blacksmithing classes.
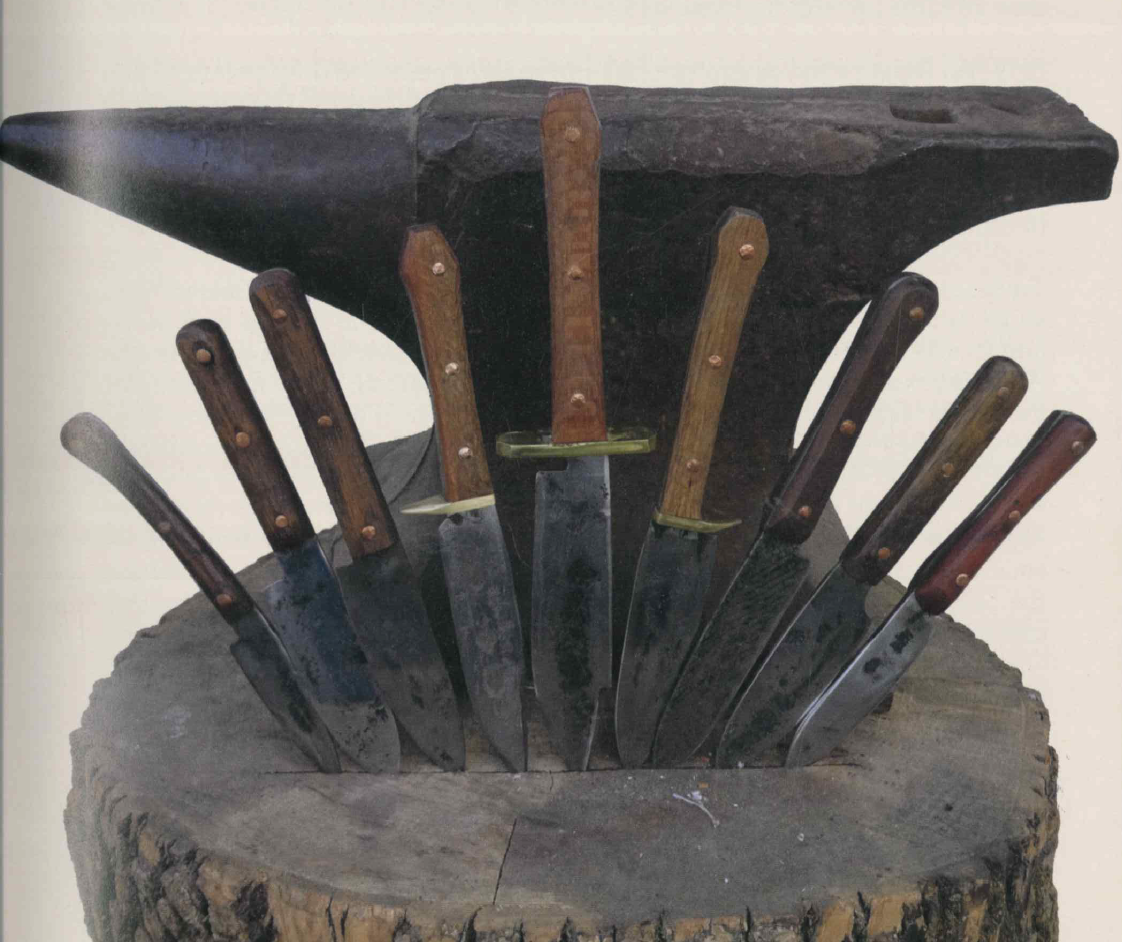
About Paul White
Paul White, Blacksmith and knife-maker, has forty plus years of knife-forging experience. His journey began with his exceptional good fortune by learning early from four ancient blacksmiths/knifemakers. These guys were building knives as was done before 2X72 grinders and epoxy glue. Those ageless methods taught to him by the “old ones” he now passes to other students of the knife.
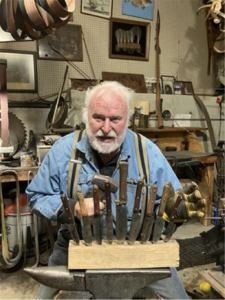
No Comments