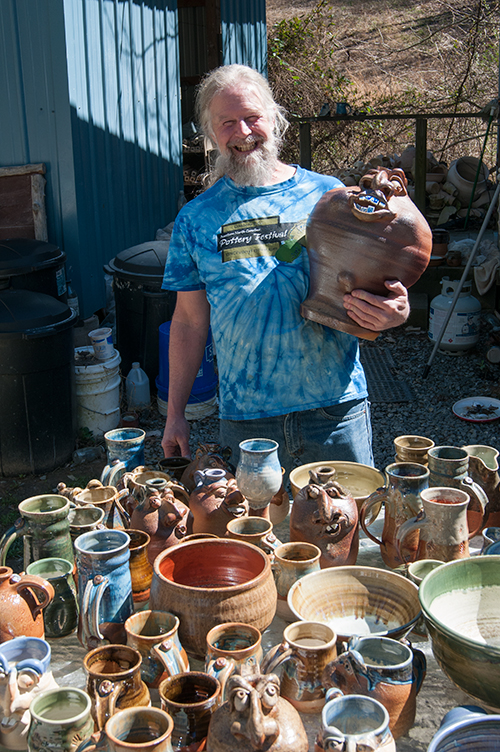
19 Mar Woodfire XIII with Rob Withrow
It’s like Christmas Eve over at Smoke in the Mountains Pottery today because it’s the day before the big wood kiln will be opened and unloaded. Many potters from all over the region contribute pots to be fired the traditional way in Rob Withrow’s huge wood kiln. This is Rob’s 13th wood firing at his studio. I stopped by and caught him taking a little peek inside the chamber and took the opportunity to talk to him about the firing and clay in general. Join us in the sneak peek…
CP: So what are you doing right now?
RW: I’m unbricking this kiln here that’s been cooling for five days. We heated it up to 2500 degrees using only wood, and now it’s like Christmas! You open it up and see what’s inside and this time the kiln fired so beautifully; it’s such a joy.
CP: Nice, How many time have you fired this kiln?
RW: It’s been a hard road but I stuck with it, and by golly the community came forth and helped me all along the way. I fired it nine times unsuccessfully. A weaker man would have caved or a smarter man would have stopped, but I kept going and here we are! The community came together and knew I was having problems. We put a new chimney on it and it works like a charm now. Now it’s a third of the wood, and a third of the time (than when we first started).
CP: How many times have you successfully fired it?
RW: This is number thirteen I am unloading, so four times without a hitch. The first nine times I had to unload it and re-fire everything. It was emotionally and financially draining. All the trial and error was worth it though. Now you look in here and the pots are just beautiful–they’re glowing! It’s just what I dreamed!
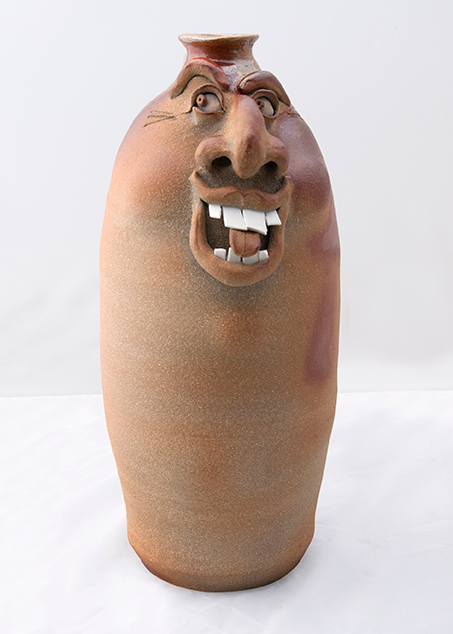
Not quite a 6-footer, but still a Large Face Jug by Rob Withrow, Wood Fired at Smoke in the Mountains, March 2015.
CP: You are known for throwing really tall face jugs. Do you have one in this firing?
RW: My passion is 6ft. pots. With the wood kiln, I can roll a 6 ft pot right in the chamber. This time it just fell over! I got the handle on it, signed it, it had an iguana on the top, and it just fell like a tree (laughs) you gotta be ready for that. That’s gonna happen every once in a while, if it was easy everyone would be doing it. You try to figure out why it happened and you just gotta know the next one will be better. There’s a lot of “ups”and “downs” in this business, but the “ups” are really up.
CP: Who was involved in this wood firing?
RW: Many different potters load pots and help with the firing. These folks had pots this time around: Harry and Julie B. Hearne (Turning Point Clay Studio, Brasstown, NC), Ted Cooley and Hannah Levin Cooley (Winding Stream Studio, Brasstown, NC), Chris Jones (Murphy, NC), Walter Aberson and Joyce Branch (Concord, NC), Evan Allhands (The Allhands Pottery, Cinncinatti OH) Maya Hamilton (Heritage Vision Creations, Brasstown, NC), Dick Aunspaugh (Young Harris, GA), and Ian my current apprentice who is completing a High School exit project.
CP: How many pots are in here?
RW: About 700 pots. Some are this big (points to a tiny thimble size bowl) and some are this big (points to his big pig bank).
I am really pleased. Everything I am seeing right now looks really good. Everyone worked so hard. We all take shifts and put wood in every 3-5 minutes for 28 hours. The new chimney is remarkable and has really cut down on the firing time.
My pots from this firing are headed to north of Chicago where I am going to have a show and a workshop hosted by Jill Tortorella of Antioch Pottery.
(Clink)
RW: Did you hear that? A pot just broke.
CP: Is that because you opened the bricks?
RW: Well it’s cool in here, so I’m not sure why that happened. That was a pot breaking though (laughs). Some of these are re-fired, so that might have something to do with it.
CP: So wood kilns are the traditional way of firing, right? And the NC has a rich pottery tradition? Can you talk about this?
RW: Yep, North Carolina does indeed have a rich history in pottery. From the 1700s we’ve be high firing pottery in NC. The Germans and the Irish brought the technology over with them. And they were salt glazing in Seagrove “Jugtown,” NC.
They had a traditional kiln called a “groundhog kiln.” I think the potters must have been bald, so they looked like little ground hogs coming out (laughs). This type of kiln is partly buried and has a real low arch, so you put your big pots in the middle and your smaller pots out to the side. It doesn’t have any shelves on it and it just sits on old flint and sand.
Burlon Craig was North Carolina’s last remaining Folk Potter doing things the traditional way. He would make his own glaze. To tell the temperature, he would let some glaze dry out and make a cone out of it. We he fired, he would watch the cone and know when it was done. They would also hook a pot and pull it out and look at it. That pot would be ruined but they’d know how the glaze was doing.
In NC, we have really educated buyers and they really appreciate pottery. Also in North Georgia, South Carolina and into Texas there is a wide band of natural clay, so that is where big pottery centers were located.
CP: What inspired you to build a wood kiln?
RW: I learned most of my trade at the Folk School. I did a wood firing class at the Folk School with Ben Owens III and Charlie Liddell and then I just got hooked. The first time I saw the pots come out I knew that’s what I want to do. I fashioned this kiln after the Folk School kiln, I just super-sized it. So the first chamber is alot like their first chamber, just a lot bigger.
It’s a lot of work, but the results are just so beautiful that its worth all the labor. Every bowl and every mug has to be raised up off the shelf and sit on on little clay balls to keep it up so the ash from the burning wood doesn’t melt and weld it to the shelf. It’s a lot of labor. But it’s a sweet looking kiln. I look in there and it is just beautiful. And the back chamber will be even prettier because it got hotter.
This is a dream come true. I learned my whole trade at the Folk School. You could learn so many different trades there and now I get to go back and teach. I will be there till midnight many times because someone did that for me.
CP: How was your recent class?
RW: Oh we had a wonderful class! We had 11 students and Darrell Adams came and his grandpa was Bill Gordy a famous Folk Potter. I just love Darrell and it’s a pleasure to hand out with him for a week, He’s just a world of knowledge. He brings his ball mill and makes glaze out of rock. It was just a great firing we had. Evan Allhands was in that class and then we came over here and we loaded this one. I’m already excited to fire up the next one. I just cna’t get enough of it.
CP: Why so you like face jugs so much?
RW: Well everyone’s done faces. Every culture that’s ever done clay has done faces. Your just looking at them all the time, so you are bound to put one on your pot. Our tradition here in the South started with slave potters. Some potters thought that the face on the jug kept the kids out of the moonshine, but I know that would be the first jug I’d go to if it had a face on it. So I don’t think that’s true.
I just love faces and now I’m doing these face mug parties. I just had 24 kids over here this morning, from Brevard. I make a blank mug on the wheel and then I show them how I put a face on. No one ever listens to me though because they are all different (laughs). And they’re all just so cool. They did great work.
It’s amazing what people will do when you put clay in their hands. I think people are deprived of creativity and are deprived of touching the earth. I think that’s what’s gassing them. I just make it happen… getting people in the clay. It’s amazing what they come up with.
CP: Do you have any advice to aspiring potters?
RW: Make a lot of pots, that’s always been my theory! You are gonna make a thousand of crappy pots, so the sooner you get past them, the better off you are going to be. The more you deal with clay, the better you are going to get. I’ve been at it for 18 years and I’ll always be a student of clay. I just keep improving every year. It’s a lot of work and you have to be a self-starter, but I wouldn’t trade it for anything. I wake up everyday with a smile on my face and that’s straight from the heart.
Visit Rob online on his website or on Facebook.
jim mcdowell
Posted at 14:00h, 24 MarchI would love to take part in one of your wood firing.I have done some in the past and I have expirence in the process.
Cory Marie Podielski
Posted at 12:01h, 12 AprilI will forward your message to Rob, but he’s not much of a corresponder. I would got to his studio and meet him in person, if you can ever make it down to Brasstown, he is very friendly and welcoming.